Le Just-in-time (JIT) représente une révolution dans le monde de la gestion de production industrielle. Née au Japon dans les années 1950, cette méthode a transformé radicalement l’approche des entreprises concernant leurs processus de fabrication et la gestion des stocks. Plutôt que d’accumuler d’importantes quantités de matières premières et de produits finis, le JIT propose une approche minimaliste où la production s’effectue uniquement en fonction des besoins réels et immédiats. Cette philosophie de gestion permet d’optimiser les ressources, de minimiser les coûts et d’améliorer significativement la qualité des produits tout en réduisant les délais de livraison.
La méthode JIT s’inscrit dans une démarche globale d’amélioration continue et de recherche d’excellence opérationnelle. En éliminant les gaspillages sous toutes leurs formes, elle permet aux entreprises d’atteindre un niveau de performance supérieur et de gagner en compétitivité sur des marchés de plus en plus concurrentiels. De nombreuses organisations à travers le monde ont adopté cette approche et l’ont adaptée à leurs spécificités, prouvant ainsi sa pertinence et son efficacité dans des contextes variés.
Les principes fondamentaux du just-in-time (JIT)
Définition et origine du système JIT dans l’industrie automobile japonaise
Le Just-in-time, également connu sous l’acronyme JIT, est une méthode d’organisation et de gestion de la production qui vise à produire exactement ce qui est nécessaire, au moment où c’est nécessaire, et dans les quantités requises. Cette approche a été développée au Japon dans les années 1950, principalement au sein de Toyota, sous l’impulsion de Taiichi Ohno, souvent considéré comme le père de cette philosophie.
À l’origine, le JIT a été conçu comme une réponse aux contraintes spécifiques du marché japonais de l’après-guerre : des ressources limitées, un espace restreint et un besoin impérieux de reconstruire l’économie du pays. Toyota a alors développé ce qui est devenu le Toyota Production System (TPS), un ensemble de principes et de techniques visant à optimiser les processus de production tout en minimisant les coûts.
Le JIT s’inscrit dans une philosophie plus large, connue sous le nom de Lean Manufacturing (production allégée), qui cherche à éliminer systématiquement toutes les formes de gaspillage dans les processus de production. Au fil du temps, cette méthode s’est répandue dans le monde entier et a été adoptée par des entreprises de divers secteurs, bien au-delà de l’industrie automobile.
La philosophie JIT repose sur un principe fondamental : produire uniquement et exclusivement ce que le client demande, dans les délais et les quantités demandés. C’est le rêve de tout responsable de production : disposer d’un système si flexible et élastique qu’il s’adapte à la demande à tout moment.

La logique « pull » vs « push » dans la production
Le JIT introduit un changement fondamental dans la façon dont les entreprises abordent leur production, en passant d’un système « push » (pousser) à un système « pull » (tirer). Cette distinction constitue l’un des piliers conceptuels du Just-in-time.
Dans un système traditionnel de production « push », les produits sont fabriqués en fonction des prévisions de la demande, souvent bien avant que les clients ne passent commande. Les marchandises sont ainsi « poussées » vers le marché, ce qui entraîne généralement une accumulation de stocks à différents niveaux de la chaîne d’approvisionnement. Cette approche génère des coûts significatifs liés au stockage et présente des risques d’obsolescence des produits.
À l’inverse, dans un système « pull » caractéristique du JIT, la production est déclenchée par la demande réelle des clients. Les produits sont « tirés » par le marché, ce qui signifie qu’ils ne sont fabriqués qu’en réponse à des commandes effectives. Cette méthode permet de synchroniser précisément la production avec les besoins actuels, réduisant ainsi considérablement les niveaux de stocks et les coûts associés.
Cette inversion de la logique productive représente un changement de paradigme dans la gestion industrielle. Elle implique une coordination parfaite entre les différentes étapes du processus de fabrication, depuis les fournisseurs jusqu’à la livraison au client final, créant ainsi un flux continu et harmonieux de matériaux et de produits.
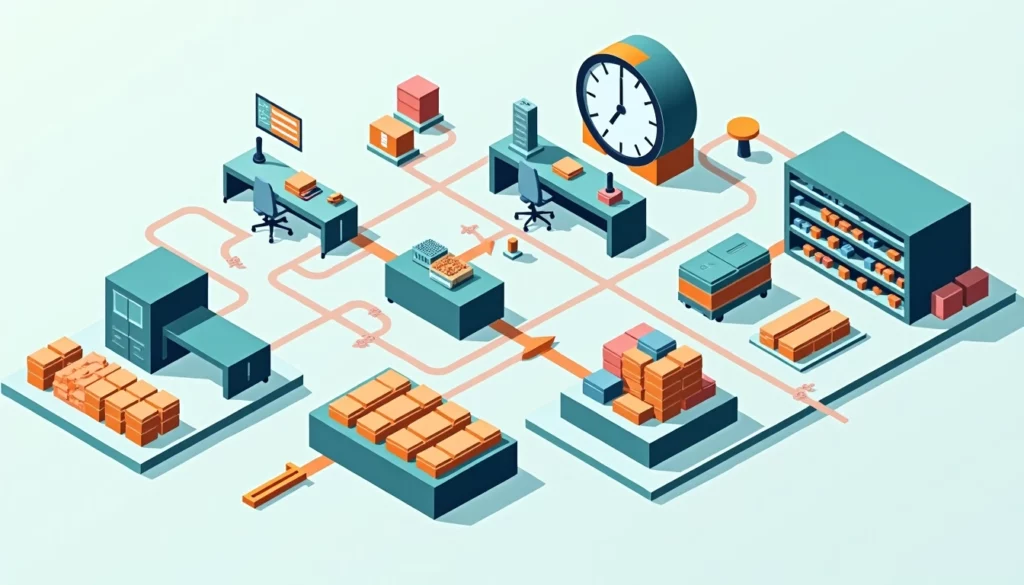
Objectifs clés : réduction des stocks et élimination des gaspillages
Le Just-in-time poursuit deux objectifs majeurs qui sont étroitement liés : la réduction drastique des stocks et l’élimination systématique des gaspillages sous toutes leurs formes. Ces objectifs constituent l’essence même de cette approche et déterminent les différentes pratiques qui en découlent.
La réduction des stocks est considérée comme l’un des principes fondamentaux du JIT. Dans cette perspective, les stocks sont perçus comme un coût à éliminer plutôt que comme un actif. Lorsque des matières premières ou des produits restent en stock, ils ne génèrent aucune valeur ajoutée mais engendrent des coûts d’entreposage, d’assurance, de manutention et risquent de devenir obsolètes. Le JIT vise donc à limiter au strict minimum les niveaux de stocks à tous les stades de la production.
L’élimination des gaspillages constitue le second pilier du JIT. La philosophie japonaise identifie sept types de gaspillages (muda) à combattre :
- La surproduction (produire plus que nécessaire ou avant que ce soit nécessaire)
- Les attentes (temps d’inactivité des personnes, des machines ou des produits)
- Les transports inutiles (déplacements superflus de matériaux)
- Les traitements inappropriés (processus trop complexes ou inutiles)
- Les stocks excessifs (accumulation de matières et produits)
- Les mouvements inutiles (déplacements non nécessaires des opérateurs)
- Les défauts (production de pièces non conformes nécessitant retouche ou rebut)
En ciblant ces différentes formes de gaspillage, le JIT permet aux entreprises de rationaliser leurs processus, d’améliorer leur efficacité opérationnelle et de réduire significativement leurs coûts de production. Cette approche conduit également à une meilleure qualité des produits et à une plus grande satisfaction des clients.
Différence entre le JIT et le JIC (Just-in-Case)
Le Just-in-Case (JIC), ou « juste au cas où », représente l’approche traditionnelle de gestion des stocks, diamétralement opposée au JIT. Il est essentiel de comprendre les différences fondamentales entre ces deux philosophies pour saisir pleinement l’impact transformationnel du Just-in-time.
Le modèle JIC repose sur une logique de précaution et de sécurité. Il consiste à maintenir des niveaux de stocks importants pour se prémunir contre d’éventuelles ruptures d’approvisionnement, fluctuations imprévues de la demande ou problèmes de production. Cette méthode donne la priorité à la gestion des risques, souvent au détriment de l’efficacité opérationnelle et de l’optimisation des coûts.
À l’inverse, le just-in-time privilégie la minimisation des stocks et la production en flux tendu, synchronisée avec la demande réelle. Le tableau ci-dessous illustre les principales différences entre ces deux approches :
Critère | Just-in-Case (JIC) | Just-in-Time (JIT) |
---|---|---|
Niveau des stocks | Élevé | Minimal |
Taille des lots de production | Grands lots | Petits lots |
Pilotage de la production | Basé sur les prévisions | Basé sur la demande réelle |
Gestion des risques | Par les stocks tampons | Par la flexibilité et la réactivité |
Coûts de stockage | Élevés | Faibles |
Détection des problèmes | Souvent masqués par les stocks | Immédiatement visibles |
Le JIT est devenu la norme industrielle moderne au cours des dernières décennies, principalement en raison de ses avantages en termes de réduction des coûts et d’amélioration de l’efficacité opérationnelle. Cependant, comme la crise sanitaire mondiale l’a démontré, une approche hybride combinant certains aspects du JIT et du JIC peut parfois s’avérer plus pertinente, notamment dans des contextes d’incertitude élevée ou de chaînes d’approvisionnement complexes.
Mise en œuvre des techniques JIT en entreprise
Le système kanban : gestion visuelle des flux de production
Le système Kanban constitue l’un des outils fondamentaux pour la mise en œuvre concrète du Just-in-time. Développé par Toyota dans les années 1950, ce terme japonais signifiant « carte » ou « signal visuel » désigne une méthode de gestion visuelle des flux qui permet de piloter efficacement la production en fonction de la demande réelle.
Le principe du Kanban est relativement simple : des cartes ou signaux circulent entre les différents postes de travail pour indiquer précisément quand et quelle quantité produire. Chaque carte représente une autorisation de production ou de transfert d’une quantité définie de pièces ou de produits. Aucune production ne peut être lancée sans la présence d’une carte Kanban, ce qui garantit que la fabrication est strictement alignée sur les besoins réels.
Ce système fonctionne selon une logique de « supermarché » : lorsqu’un client (interne ou externe) prélève un produit, il déclenche automatiquement le réapprovisionnement de ce même produit. Le Kanban sert ainsi de signal pour indiquer au poste en amont qu’il doit produire pour remplacer exactement ce qui a été consommé, ni plus ni moins.
Dans un environnement moderne, le Kanban physique (cartes papier) a souvent été remplacé ou complété par des systèmes électroniques (e-Kanban) qui permettent une transmission instantanée des informations et une gestion plus flexible des flux. Ces systèmes s’intègrent parfaitement aux solutions informatiques de gestion de la production et contribuent à l’optimisation globale de la chaîne logistique.
La mise en place d’un système Kanban efficace permet non seulement de réduire significativement les niveaux de stocks intermédiaires, mais aussi d’identifier rapidement les goulets d’étranglement et autres dysfonctionnements dans le processus de production. C’est un outil puissant de visualisation des flux qui facilite l’amélioration continue des processus.
SMED : réduction des temps de changement pour la production en petites séries
Le SMED (Single Minute Exchange of Die), ou « changement d’outil en moins de dix minutes », est une méthode essentielle dans l’arsenal des techniques JIT. Développée par Shigeo Shingo pour Toyota, cette approche vise à réduire drastiquement les temps de changement d’outils ou de séries sur les équipements de production.
Dans un environnement JIT où la production s’effectue en petites séries pour suivre au plus près la demande, les changements fréquents de séries peuvent représenter un défi majeur. Traditionnellement, ces opérations nécessitaient plusieurs heures, rendant peu rentable la production de petits lots. Le SMED propose une méthodologie structurée pour minimiser ces temps improductifs .
La démarche SMED s’articule autour de plusieurs étapes clés :
- Identifier et séparer les opérations internes (qui nécessitent l’arrêt de la machine) des opérations externes (qui peuvent être réalisées pendant que la machine fonctionne)
- Convertir le maximum d’opérations internes en opérations externes
- Rationaliser et simplifier toutes les opérations (internes et externes)
- Standardiser les procédures et former les opérateurs
- Automatiser certaines opérations lorsque c’est pertinent
Grâce à cette méthode, des entreprises ont réussi à réduire leurs temps de changement de plusieurs heures à quelques minutes, voire secondes dans certains cas. Cette performance permet de produire économiquement en petites séries, augmentant considérablement la flexibilité de la production.
Le SMED contribue également à réduire le BFR (Besoin en Fonds de Roulement) des entreprises en diminuant les stocks et en accélérant la rotation des produits. Cette technique s’avère particulièrement précieuse dans les industries confrontées à une grande diversité de produits ou à des cycles de vie courts.
Standardisation et amélioration continue des processus
La standardisation des processus constitue une condition préalable essentielle à la mise en œuvre efficace du Just-in-time. Elle consiste à définir et documenter les meilleures pratiques pour réaliser chaque tâche, créant ainsi une référence commune pour tous les opérateurs. Cette standardisation permet d’assurer la constance de la qualité, la prévisibilité des résultats et l’identification rapide des anomalies.
Dans l’environnement JIT, les standards ne sont pas figés mais évoluent constamment grâce au Kaizen , principe japonais d’amélioration continue. Cette dé
Élimination des 7 types de gaspillage
marche combine le concept de standardisation avec une approche systématique d’élimination des gaspillages. Les sept types de gaspillage identifiés dans le système Toyota (muda) font l’objet d’une attention particulière et d’actions spécifiques :
Pour chaque type de gaspillage, des outils et méthodes dédiés sont mis en place. Par exemple, la surproduction est combattue par l’utilisation du système kanban, tandis que les temps d’attente sont réduits grâce à l’équilibrage des lignes de production et à la mise en place de flux continus. Les défauts sont traités à la source grâce à des systèmes anti-erreur (poka-yoke) et une maintenance préventive rigoureuse.
Organisation et nettoyage du poste de travail (5S)
La méthode 5S constitue un pilier fondamental de l’organisation du travail dans un environnement JIT. Cette démarche structurée en cinq étapes (Seiri, Seiton, Seiso, Seiketsu, Shitsuke) vise à créer et maintenir un environnement de travail propre, ordonné et efficace.
Les 5S se déclinent ainsi :- Seiri (Débarrasser) : Éliminer tout ce qui est inutile sur le poste de travail- Seiton (Ranger) : Organiser l’espace de travail de manière efficace- Seiso (Nettoyer) : Maintenir la propreté et l’ordre- Seiketsu (Standardiser) : Formaliser les règles et procédures- Shitsuke (Suivre) : Maintenir durablement la démarche
Technologies et systèmes d’information soutenant le JIT
La mise en œuvre efficace du JIT s’appuie aujourd’hui largement sur des solutions technologiques avancées. Les systèmes ERP (Enterprise Resource Planning), MES (Manufacturing Execution System) et autres outils de pilotage en temps réel permettent une gestion précise des flux et une coordination optimale entre les différents acteurs de la chaîne de production.